Our Technology
Nach Jahren der Innovation und Entwicklung steht Steinmüller Babcock Environment dank eines Heeres erfinderischer Köpfe mit einem endlosen Drang, unerforschtes, geistiges Terrain zu erschließen, an der Spitze der Technologie. Wir werden diesen technologischen Fortschritt fortsetzen und uns bemühen, unsere Aufgabe zu erfüllen, den Abfall zu beseitigen, den andere hinterlassen.
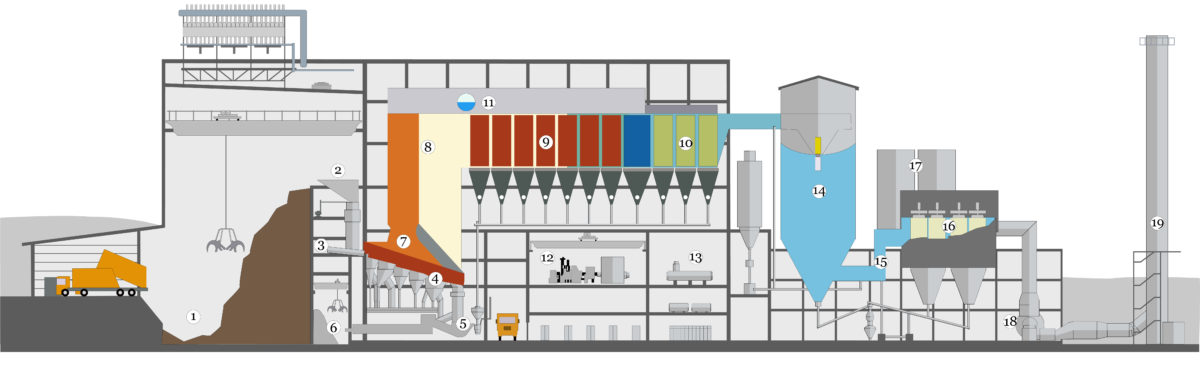
Abfallbunker: Der angelieferte Abfall wird im Abfallbunker (1) gelagert und durch den Kran homogenisiert. Der Kran transportiert dann den gemischten Abfall zum Aufgabetrichter (2) . Über die Rutsche gelangt der Abfall zum Aufgeber (3), der den Abfall entsprechend den Anforderungen der Feuerungsregelung auf den Verbrennungsrost schiebt.
Vorwärtslaufender Rost: Der Abfallverbrennungsprozess findet auf dem Rost (4) statt, der aus Roststabreihen mit nebeneinanderliegenden Roststäben besteht. Die Roststabreihen sind überlappend hintereinander angeordnet. Jede zweite Reihe bewegt sich abwechselnd vor und zurück. Der Abfall und später das Schlackenmaterial wird durch diese Reihen zum Ende des Rostes transportiert, wo die Schlacke in den Schlackenabzug (5) ausgetragen wird.
Schlackeabsauger: Der Schlackenabzug (5) ist teilweise mit Wasser gefüllt, wodurch ein Luftabschluss zwischen der Umgebung und dem Ofen selbst entsteht. Die vom Rost fallende Schlacke wird im Wasserbad abgekühlt und durch den Stößel des Schlackenabzuges auf einen Schwingförderer befördert, der die Schlacke in den Schlackenbunker (6) transportiert.
Feuer auf dem Rost: Die Anlagenbetreiber überwachen den Verbrennungsprozess auf dem Rost (7) via Kamerasystemen. Die zur Verbrennung benötigte Luft (Primärluft) wird kontrolliert von unten durch den Rost zugeführt. Um einen optimalen Ausbrand der Rauchgase zu erreichen, wird zusätzliche Luft (Sekundärluft) oberhalb des Rostes eingeblasen. Im Kessel werden die heißen Rauchgase dann auf die jeweils gewünschte Rauchgasaustrittstemperatur abgekühlt.
Kessel: Die Wärme der Rauchgase wird genutzt, um demineralisiertes Wasser in den Economiser-Heizflächen (10) zu erhitzen. Dieses sogenannte Kesselspeisewasser wird dann in die Trommel (11) geleitet, die den Verdampfer speist.
Das in den Wänden der Kesselstrahlzüge (Verdampfer) (8) entstehende Wasser-Dampf-Gemisch wird in der Trommel in Wasser und Dampf (11) getrennt. Der Dampf wird zu den Überhitzerheizflächen (9) geleitet. Nach dem Aufheizen auf die vorgegebene Temperatur wird der frische Dampf zur Turbine (12) geleitet.
Turbine: In der Turbine (12) wird der überhitzte Dampf entlastet, um den Rotor der Turbine zu drehen, und anschließend kondensiert. Die dabei freiwerdende Energie wird im angeschlossenen Generator zur Stromerzeugung genutzt. Der Strom wird in das öffentliche Netz eingespeist. Das Kondensat wird im Speisewasserbehälter (13) gesammelt und schließlich dem Kessel wieder zugeführt. Alternativ kann ein Teil der Energie in Nah- oder Fernwärmenetze eingespeist oder als Prozessdampf genutzt werden (Kraft-Wärme-Kopplung).
Sprühabsorber: Im Sprühabsorberaufsatz (14) werden Wasser und Kalkmilch in das Rauchgas aus dem Kessel eingeführt. Während des Fluss durch die Absorberkühlung werden optimale Reaktionsbedingungen für die Abscheidung insbesondere der sauren Schadstoffe erreicht. Nach der Abkühlung des Rauchgases werden im Kreislauf (Reaktionsprodukte werden im Gewebefilter abgeschieden) frisches, trockenes Absorptionsmittel und Aktivkohle in den Flugstromreaktor (15) eingeführt.
Gewebefilter: Die im Rauchgas noch enthaltenen Schadstoffe reagieren chemisch oder werden von den Feststoffen adsorbiert und dadurch mit der Flugasche im nachfolgenden Gewebefilter abgeschieden (16). Als Filtermedium sorgen mehrere tausend Filterschläuche dafür, dass das gefilterte Rauchgas sicher allen gesetzlichen und umwelttechnischen Anforderungen entspricht. Ein hoher Anteil der Reaktionsprodukte wird vor dem Gewebefilter rezirkuliert. Zur optimalen Ausnutzung der Einsatzstoffe kann das Rezirkulat befeuchtet werden. Ein Teilstrom der Reaktionsprodukte wird kontinuierlich ausgetragen und zur Entsorgung in Silos (17) gefördert.
ID-Ventilator: Der ID-Ventilator 18 hält den Unterdruck im Verbrennungsprozess aufrecht und führt das Rauchgas durch den Kessel und die Rauchgasreinigungsanlage. Der Unterdruck sorgt auch für die Dichtheit des Systems bezüglich des Rauchgases.
Schornstein: Das gereinigte Rauchgas verlässt den Prozess über den Schornstein in die Atmosphäre (19). Um die Effizienz weiter zu verbessern, werden in Müllverbrennungsanlagen immer mehr Kondensationswärmetauscher installiert. Das bedeutet, dass sauberer, reiner Wasserdampf in Form von weißen Wolken aus dem Schornstein austritt und sich auflöst – ein Zeichen für optimale Energieausnutzung.
“Vorsichtige Schätzungen gehen davon aus, dass die energetische Nutzung von Abfällen heute im Durchschnitt eine Menge an fossilen Brennstoffen einspart, die dem Bedarf von rund 700.000 Bürgern entspricht.”
WIR ENTWICKELN GESTALTEN UNTERSTÜTZEN ERSCHAFFEN DIE ZUKUNFT
FULL OF ENERGY
STEINMÜLLER BOILER
Der Steinmüller Kessel wird insbesondere für die Rückgewinnung von Energie genutzt, da der Kessel in der Lage ist, Wärme über ein komplexes System auszutauschen, das für den Betrieb unter Bedingungen hinsichtlich Korrosion, Verschmutzung, Verschlackung, Belastung, Teillastverhalten und Systemdynamik ausgelegt ist.
ALWAYS ON FIRE
VERSA GRATE
Die Leistung Ihrer Anlage hängt stark von ihren inneren Komponenten ab, und hier kommt unser Vorschubrost ins Spiel. Als zentrale Komponente im “Waste to Energy”-Prozess, ob luft- oder wassergekühlt, erreicht der Rost wundersame Transformationen.
OUT OF THE ASHES
DRY X TRACT
Die Müllverbrennung verdeutlicht den Reichtum an Ressourcen, die zur Rückgewinnung zur Verfügung stehen. Bei der Behandlung wird nicht nur thermische Energie zurückgewonnen, sondern es bleiben auch Reststoffe, wie Asche und Schlacke, zurück. Diese Feststoffe machen etwa 25 % des Rohmülls aus. Ein großer Teil kann jedoch mit Hilfe unseres Dry X Tract Systems wiederverwertet werden.
ALWAYS ON
TRUE VIEW
Dank unseres True View Systems garantiert Steinmüller Babcock Environment den Spitzenbetrieb des Rostes und eine extrem lange Lebensdauer der Anlagen.
FIRE CONTROL
ACTIVE IGNITE
Zur Optimierung und Überwachung der Verbrennung in der Anlage wurde das Steinmüller Babcock Active Ignite System entwickelt. Um einen möglichst hohen Wirkungsgrad zu erreichen und Schwachstellen aufzudecken, passt sich das System automatisch an steigende Brennstoffmengen an.